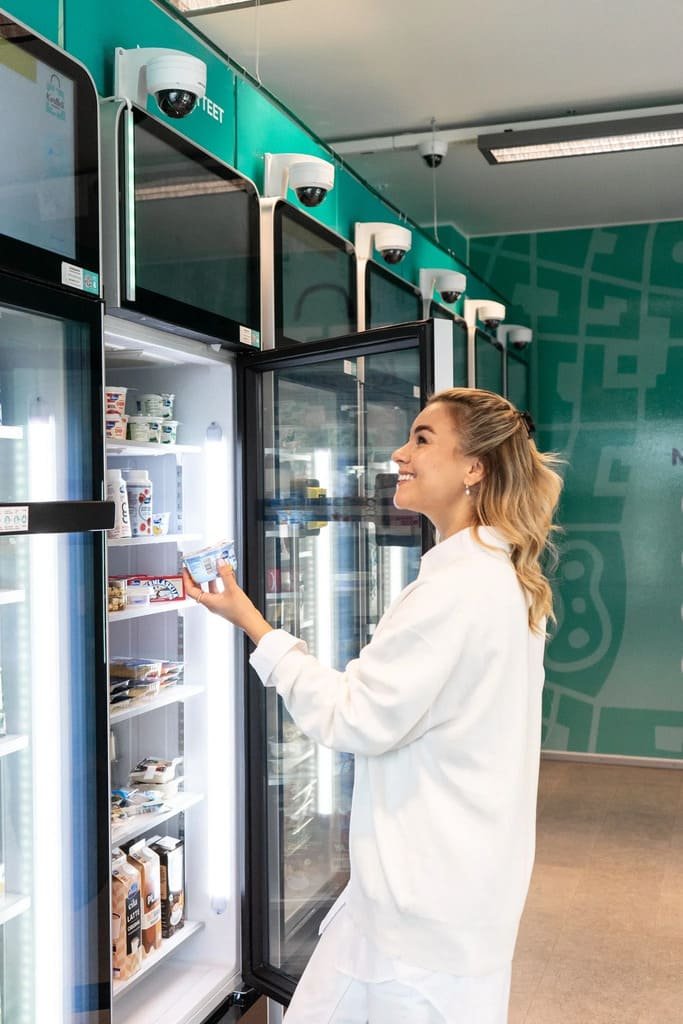
Smart Industries
Inspiring Leap into the Grocery Business with RFID Technology
Smart Industries
Technology adopted in the production line control guarantees 100% safety on shipping the products to the customers
In another pioneering initiative in the global furniture industry, Florense adopted the RFID (radio frequency identification) system on the parts that make up each order to ensure that each item will be shipped correctly and will be in accordance with the respective batch to be manufactured and delivered. But to reach this degree of applied technology, Florense has been on a long journey. "As a small joinery established in 1953, the part control was made in an equally handcrafted way. However, with the beginning of mass furniture production in the 1960s, this control began to require greater care. But the market did not yet offer a digital control system," recalls Felipe Corradi, Industrial Director and CTO at the furniture company.
The need became more imminent in 1975, when Florense inaugurated an automated factory with a very high production capacity, which increased the need for a digital shipping control. The bar code emerged exactly at that decade. "The system worked for a while, but the growing demand over the following decades triggered the need for a faster system to scan the parts and minimize shipping errors.”
The solution came two and a half years after much research as a joint development by Florense with AKR Sistemas, responsible for the integration, and with Beontag, owner of the RFID technology. "Finally, we were ready to be pioneers in the global furniture industry to deploy the RFID system. A necessary evolution, since at the beginning of the year (2022), when the system was installed, the plant already dealing with approximately 190,000 items monthly", celebrates Felipe.
"AKR Sistemas' relationship with Florense is not new, but in the last three years it has intensified precisely due to the RFID project," says Marcos Romani, from the integrator company. He recalls that they tested several antennas in the operation until they approved the one that guaranteed total scanning.
In parallel to the new antenna, Beontag launched a RFID tag model with more efficiency on scanning depth. "Thus, we are able to scan the tags more easily, even in critical conditions. We are talking about scanning from 200 to 300 products per pallet, with each pallet corresponding to one order." To get an idea of Florense's business complexity and size, a single order may have, on average, 15,000 items.
"For this reason, the tests were extremely thorough and lasted almost six months before the system could officially roll out. We even used one person to check if the RFID count was correct. We have also had small adjustments to align the tag size, the chip position, the paper model, type of glue, and tag color”, adds Marcos.
The fact that Florense already had the practice of attaching the labels on the outside of the part, a legacy of the bar code use, made the RFID implementation easier. But while the scanning was per part in the previous system, taking about 30 minutes per pallet, with RFID the scanning time for each pallet was reduced to seconds. And when there is a wrong part on the pallet, a siren sounds, and a mobile scanner goes into operation to identify which part is not in compliance with the order. Previously, the operation of disassembling a pallet to find the wrong part would take more than one hour.
Florense has two portals, one used to assemble the order and another one to send the assembled order to dispatch. "As the next steps in this digital journey, Florense is already studying the implementation of RFID in the shipment stage, if possible, to track the product to the final customer's home, and internally, in the factory, to track each item and avoid losses or damages.
About the project difficulties, Marcos mentions the scanning obstruction by the forklift’s fork. "When the forklift truck was too close to the parts, sometimes the labels near the fork were not scanned. To solve the issue, Florense adopted larger pallets and instructed the forklift operators to pick up the pallet farthest from the fork, leaving a gap of about 30 cm between the fork bulkhead."
Another difficulty: too much power had to be given to achieve 100% scan reliability. The solution came from confining the signals as much as possible and isolating a slightly larger area.
Currently, RFID tags provided by Beontag are used in all parts of each item of manufactured furniture; the final control is done on dispatch. As immediate results of the technology adoption, Felipe Corradi, from Florense, highlights the increased safety, agility and mitigation of parts replacement for issues related to technical assistance and the interception and blocking of any possible error when separating the parts requested in the orders. Another important gain was the reduction from 30 minutes to 05 seconds in the checking time for each pallet.
The system also has audible and visual alerts in case of possible misplaced volumes; integration of visual controls with checking progress controls; and the possibility of implementing the checking sequence in the external logistics cycle - transportation and deliveries - at a low cost.
"We can also track and ascertain the location of the volumes in certain boundaries or areas and ensure significant improvements in the ergonomics of the checking activities," says Felipe.
In practice, when passing through the scanning devices installed at the beginning and end of Florense's production line, all the components of the part batch are identified by a scanner that automatically sends the information to a computer that registers it. When 100% of the order's component list is reached, the batch is released for shipping with zero risk of error.
But the results were not only visible internally at Florense. Felipe says that the company received several positive feedbacks from franchised stores, especially regarding the system accuracy, which avoids receiving orders with missing parts.
"As Florense is a company that supplies to the luxury customers, before starting the project the bar was already high, and success was a basic assumption. Identifying the items was a major challenge, because all the parts are customized per client and have no size standard. Thus, it is difficult to define schemes and scanning positions", recalls Adriana Ferreira, Brazil RFID Sales Channel Director at Beontag.
Roger Davanso, New RFID Business Manager at Beontag, adds: "To mitigate this issue, we use a Beontag inlay containing a last generation chip that guarantees 100% readability. The difficulty also comes from the fact that most items are made of wood, although there is also a lot of hardware and glass. In other words, it is again worth pointing out that there is no standard for pallet assembly. Therefore, this project can be considered a true success case, especially for maintaining balance throughout the RFID ecosystem (tag, software, hardware, and services).”
Besides all technology embedded in the Florense project, Felipe Corradi highlights the system’s importance to change the company's culture, mainly leveraged by the strategic operational gains. "This is a path with no return. The future of operations like Florense’s will certainly be more digital day after day. The maturity process itself and the learning curve created with new technologies provide better working conditions and eliminate processes and operations that do not add value to the customer."
According to the Director, for having an ongoing concern with the adoption of innovative technologies such as RFID, Florense set up a committee and a specific project on Industry 4.0, with the participation of NEO (Nucleus of Operational Engineering) from the University of Rio Grande do Sul (UFRGS), which prepared a maturity report that points out the company’s next steps.
"But this is all part of a process. We are industry pioneers in some technologies, such as RFID, but we know that we need to evolve in other areas. The important thing is that, in general, we stand our ground in this search for digitalization and new technologies," concludes Felipe.
This search undoubtedly reflects the Italian roots of this 100% Brazilian company: the passion for always making the best furniture. And to this end, some of the founding values are non-negotiable, such as the significant investments in design, in eco-friendly manufacturing processes, and in cutting-edge technology associated with craftsmanship. This philosophy has helped the brand to consolidate itself among the best high-end furniture manufacturing companies in the world.
"We have authorship items, we are a company that dominates all the industrial processes, develops exclusive technologies, always innovating and operating by the custom-made system, which means we customize each project as a great fine joinery, respecting the measuring flexibility, the variety of noble materials and the hundreds of finishing patterns”
The fatto a mano culture, combined with cutting-edge technology, makes each Florense project truly unique and the high quality is reflected in the franchisee network with more than 60 stores in Brazil, the United States and Latin America. "All this justifies the credibility and trust the brand has achieved in the luxury decoration industry in Brazil and abroad", Felipe concludes.