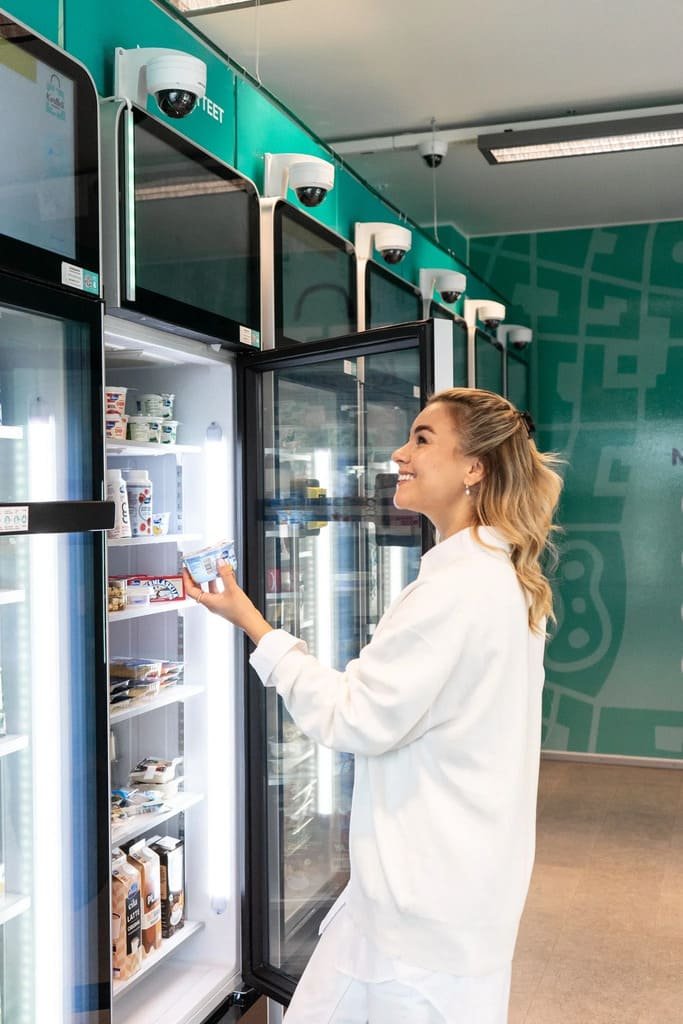
Smart Industries
Inspiring Leap into the Grocery Business with RFID Technology
Smart Industries
RFID tags enable smart manufacturing at Volvo Cars.
RFID tags enable smart manufacturing at Volvo Cars.
Applications
Challenge
Control complex product mix and manage customized parts by identifying, tracking and tracing the key items in the process flow.
Benefits
Improved utilisation of assets and resources by minimizing waiting times and eliminating waiste or re-work.
Lean operations and smart automation improve cost-efficiency and productivity.
Final products match customers’ specifications and expectations.
Car buyers today typically order a number of custom options when they make their purchase. For car manufacturers this means that many of the vehicles they produce are effectively unique. Production is further complicated since several different models are typically assembled in the same production line. To manage such a variety during production, each vehicle needs to be uniquely identified and reliably tracked throughout the process.
In response to these challenges, Volvo Car Corporation – a premium brand car manufacturer and one of the pioneers in modern automotive manufacturing – uses RFID technology to boost their automotive production. With the help of Confidex RFID tags Volvo Cars is able to track their production assets all the way from the welding and paint shop to the point of final assembly.
Previously, Volvo Cars was using three different methods for identifying and tracking each car during the production: barcode technology in the manufacturing, active RFID in the paint shop and large barcodes in the final assembly. Not only was this approach costly to maintain, but it was not sufficiently reliable for a well-balanced manufacturing process where the slightest disturbance can affect the entire throughput of the factory.
Based on Volvo Cars’ high quality and performance requirements, Confidex developed a robust passive UHF RFID tag solution capable of withstanding harsh conditions throughout the production process. After leaving the welding shop, car bodies proceed to the paint line – the most demanding environment for the tags used. On the paint line the car is put through an electrolyte bath for corrosion prevention, followed by several layers of paint and a series of high temperature drying ovens. Under these conditions, it is critical that the RFID tag’s performance does not degrade and that it retains its readability and reliability.
The Confidex Heatwave™ RFID tag is permanently mounted on the chassis of the car being manufactured at the beginning of the process, and reliably identified at various points in the manufacturing process. The tag is left on the vehicle, eliminating the need for collecting, cleaning and testing the used tags. The Confidex RFID tag has been in use at Volvo cars since 2018 and over the period has demonstrated outstanding reliability over the complete car manufacturing process, despite the complex and harsh conditions.
Confidex offers a complete portfolio of high-quality RFID tags and specialty labels designed for the automotive industry. By encoding the vehicle ID number on the tag, the solution can also be used in outbound logistics to simplify distribution of the finished cars.
Read an article about Confidex tag’s further development: New genaration RFID tags tested by Volvo Cars